Custom Built Automation Solutions
- Home
- Automation Solutions
Since our inception in 2005, we at Innomation have actively sought out challenging automation requirements and have successfully deployed a wide variety of one of a kind solutions. We’ve worked with sectors as diverse as
Satellite Communication
Engineering Components
Telecom
Bakery
Confectionery
Tobacco
Our cross-sectoral R&D expertise helps us develop out of the box solutions that set new benchmarks in productivity & quality. Many of these solutions today are a part of our product portfolio.
Our objective of being an “Equipment Lifecycle Partner” is best demonstrated with our approach towards R&D projects. Beginning with identifying automation opportunities followed by prototyping, validation, and feasibility studies, we work with our clients in identifying the best areas to automate in order to reach their business goals and ROI targets. Post this, we build and deploy the equipment after extensive testing, sometimes lasting months at our facilities during which we simulate all possible deviations and failure scenarios to ensure that our equipment not only meets but exceeds expectations.
Our service and support team with dedicated personnel for each installation further improves the ease of implementing the automation at our client’s factory. This inclusive approach helps us maximize ROI for our clients and ourselves. An example of our R&D automation capabilities is described below.
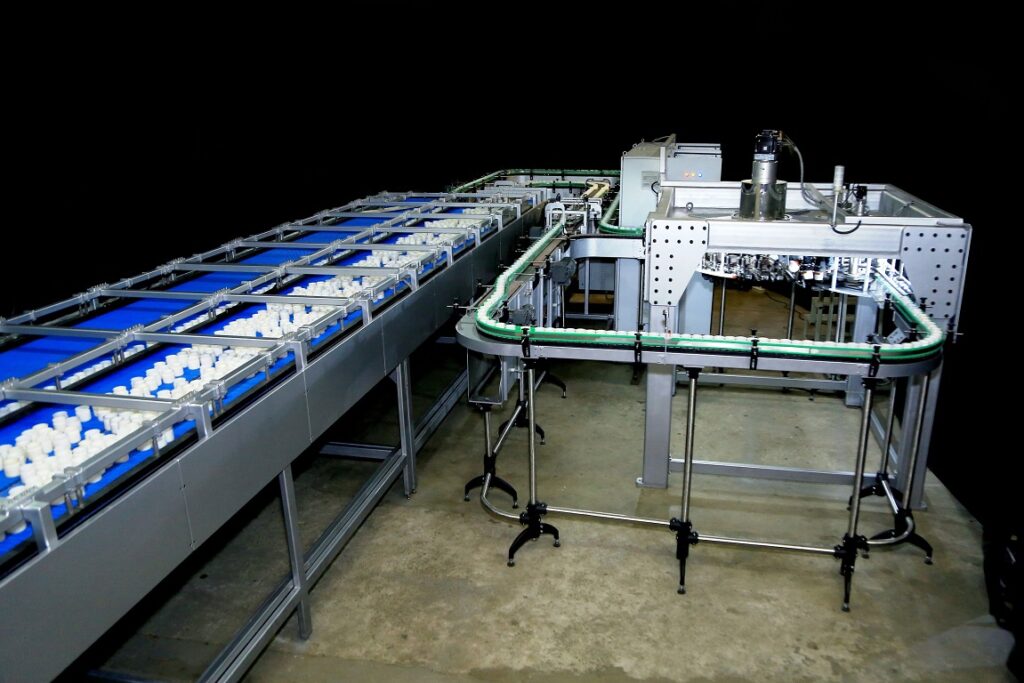
Plant Automation-Specialized Conveying Systems
Our Solution
Plastic cups called pucks are distributed on demand to each of the 24 sachet machines which deposit the required quantity of sachets into the empty pucks. The “filled” pucks are first conveyed to a buffering zone and then sequentially moved towards the secondary packaging machine where they are perfectly synchronized with the secondary packaging machine before being overturned on top of an empty pouch to empty their contents and then the empty pucks are conveyed back and distributed among the sachet packaging machines.
Multiple sensing stations coupled with a servo based motion control system ensures that the entire line is always balanced no matter how many primary packaging machines are running, or their instantaneous throughput.
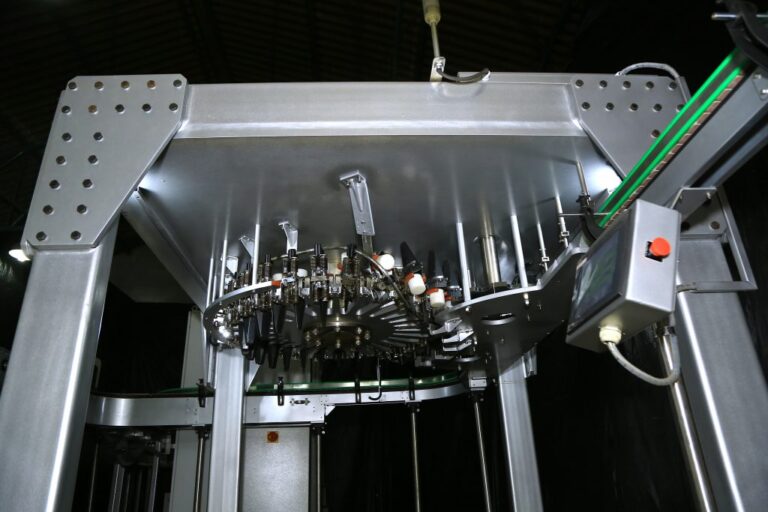
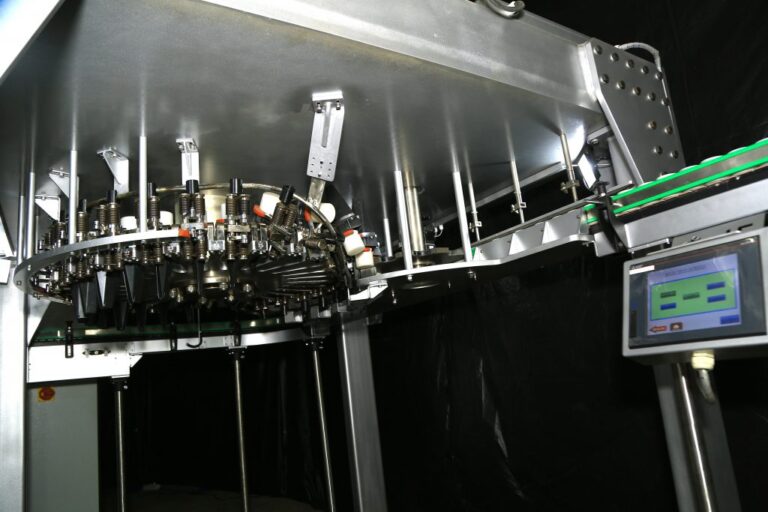
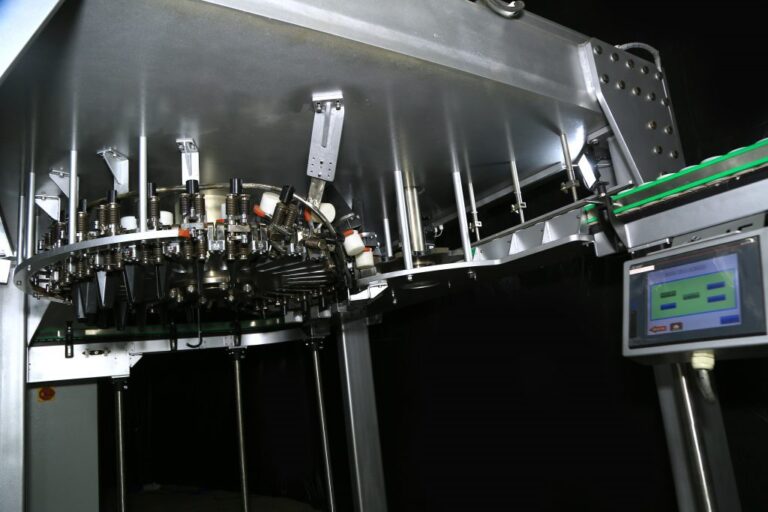
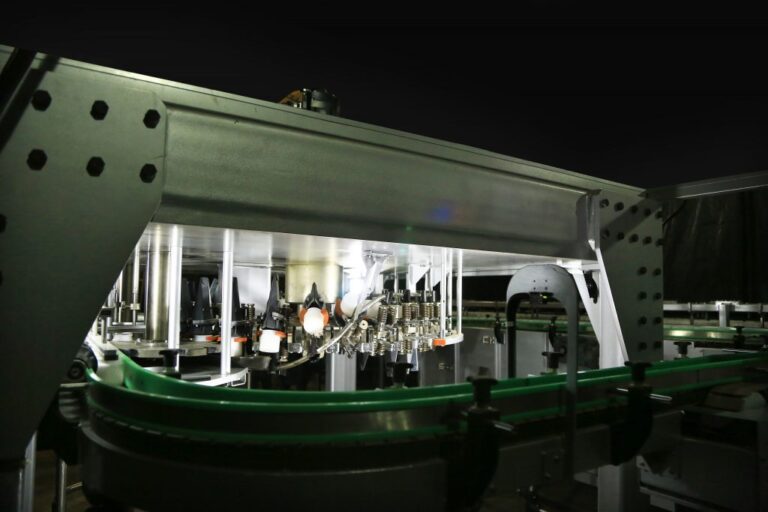
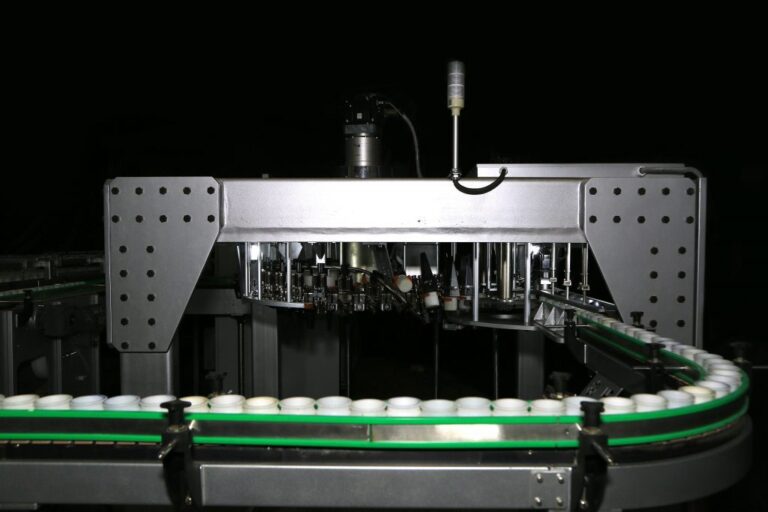
This new and innovative approach increased their entire plant’s productivity by more than 3x while drastically improving quality and reducing manpower.
Whether it comes to machines or conveyors or robotic systems, Innomation (an abbreviation for Innovative-Automation) continues to push the technological boundaries and set new benchmarks for productivity, efficiency, and quality.
How we do it
Decades of R&D experience across multiple sectors has enabled us to fine-tune our automation development process and ensure our projects meet and exceed client expectations throughout the equipment lifecycle.
Professional Automation Solutions
Our methodology is focused on partnering with our clients throughout the equipment life cycle, enabling maximum value creation. Based on decades of automation experience, Innomation has developed a tried and proven automation development process that includes all the critical steps required to ensure our projects meet or exceed customer expectations. We strive to provide a solution that:
- Exceeds the deliverables contracted
- Is user-friendly and can be easily maintained
- Is robust and stands the test of time
- Sets new benchmarks in performance, aesthetics, and safety
Innomation’s experienced and innovative teams possess the skill sets and resources required to thoroughly understand all performance requirements and budgetary constraints to develop and implement the most optimum solution for your organization.
Regardless of whether it is a custom built solution or one of our turnkey technologies, rest assured that we will exceed your expectations.