Process Automation
- Home
- Automation Solutions
- Engineering Component Automation
Ultrasonic Cleaning
Ultrasonic cleaning uses ultrasound (20 to 40kHz) to agitate a liquid and induce cavitation bubbles. This cavitation produces high localized forces and when components are passed through this agitated fluid, these localized forces dislodge contaminants thereby thoroughly cleaning the components. Unlike traditional cleaning methods, cavitation effects produced by ultrasonic cleaning also penetrate blind holes, crevices, and other difficult to reach places ensuring that the entire surface area of the component is thoroughly cleaned. A variety of fluids can be used as a cleaning agent depending on the type of contaminants and component material.
Capabilities
- Innomation can provide both batch and continuous ultrasonic cleaning equipment based on the type of component and throughput required.
- Batch ultrasonic cleaning equipment uses multiple objects placed onto open meshed trays/baskets which can be manually or semi-automatically immersed in an ultrasonic tank for a specified duration after which the cleaned objects are removed and a fresh batch is loaded.
- Continuous ultrasonic cleaning systems use trolley/hanger conveyors that continuously pick components, move them through ultrasonic tanks and deposit the cleaned components on a conveyor belt for further processing.
Unique Features
- Optional automatic dosing systems for surfactants, detergents, wetting agents, and other components.
- Optional automatic fluid heating systems for high efficiency cleaning.
- Optional vision based quality inspection post cleaning.
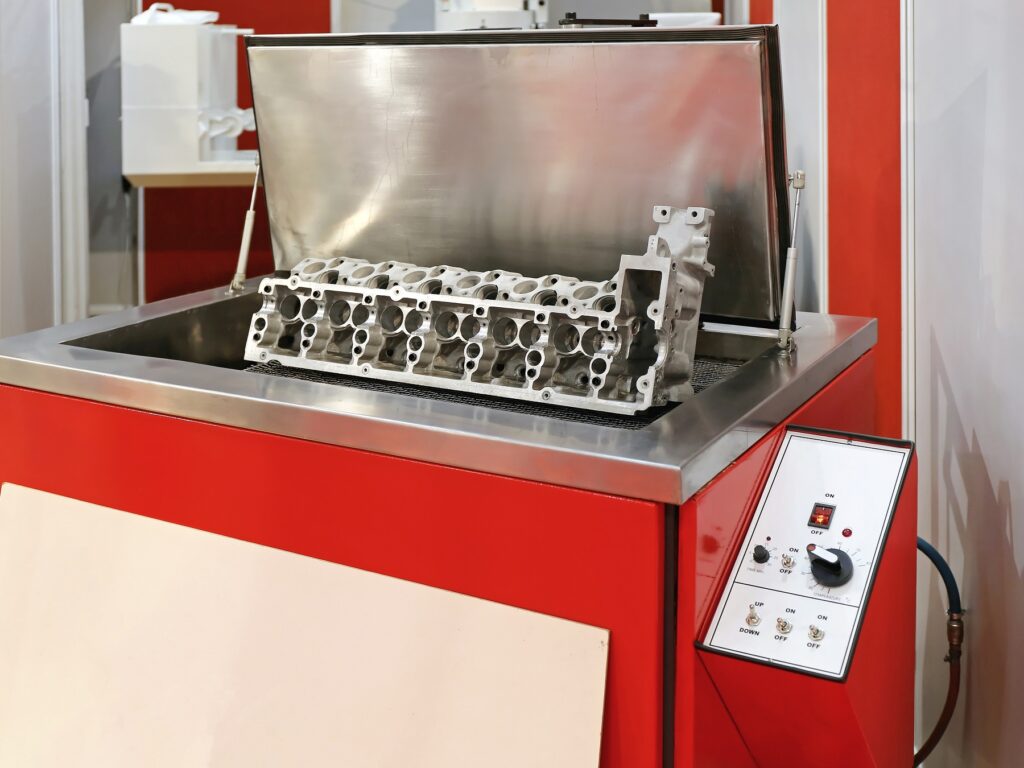
Forging Press Automation
Hot forging press shops are some of the most accident-prone areas due to the heavy equipment utilized and difficult working conditions. Innomation has designed and developed a range of forge tending automation solutions that eliminate the need for manual intervention near forging presses, thereby drastically increasing both the safety and consistency of production.
Our forge tending automation range starts with simple 3 axis manipulator arms designed to tend light and medium-duty forges up to 1000 metric tons and increases in complexity up to 6 axis multi-stage robotic arms designed to suit the heavy forging operations with multiple stroke operations.
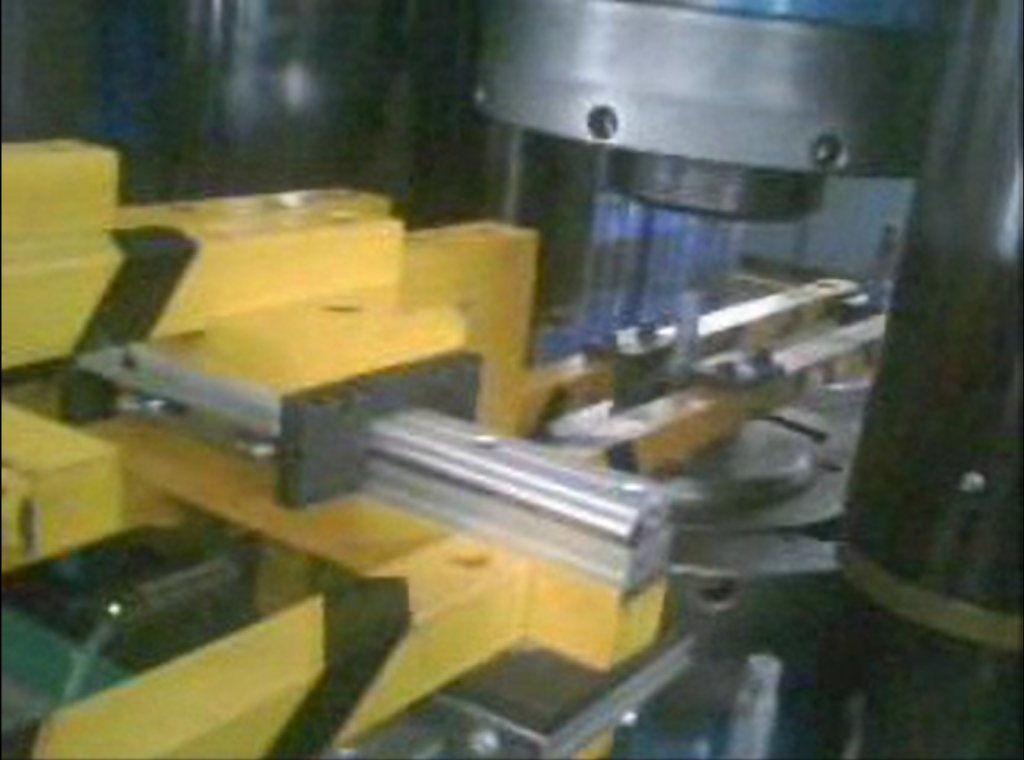
Capabilities
- Fully automated or semi-automated press tending manipulator arms to suit forging presses from 200 tons to upwards of 3000 tons.
- 3 axis, 4 axis, 6 axis manipulator arms with teach in capabilities for highly flexible and adaptive handling of components.
- Optional automatic loading and unloading systems for components.
- Optional unscrambling and sequencing systems for fully automated production.
Unique Features
- Modular gripper design enabling long term flexibility at least cost.
- Teach in capabilities enabling quick corrections and long term flexibility.
- Inbuilt crumple zones for intrinsic safety and damage limitation incase of accidents.
- Enabled with latest IoT technologies for real time full scale monitoring and control.
- Modular design enables quick re-deployment of equipment across different locations and presses by only changing the gripper and manipulator arms.
Pen Sleeving Automation
Sleeve insertion and shrink wrapping is a process in the manufacture of all kinds of sketch and marker pens. Innomation has designed and developed high speed high performance sleeve insertion and shrink wrapping line that achieves the higher quality positioning and shrink quality.
Capabilities
- Pen sizes ranging from 4mm diameter to 25mm diameter with the flexibility to handle non-symmetrical shapes and sizes.
- Throughput starting from 60 and up to 400 sleeves/minute.
Unique Features
- Linear positioning accuracy of ± 1mm.
- Vision based inspection systems and automatic rejection for reliable quality control.
- Modular gripper and sleeve holder design for flexibility and quick changeovers.
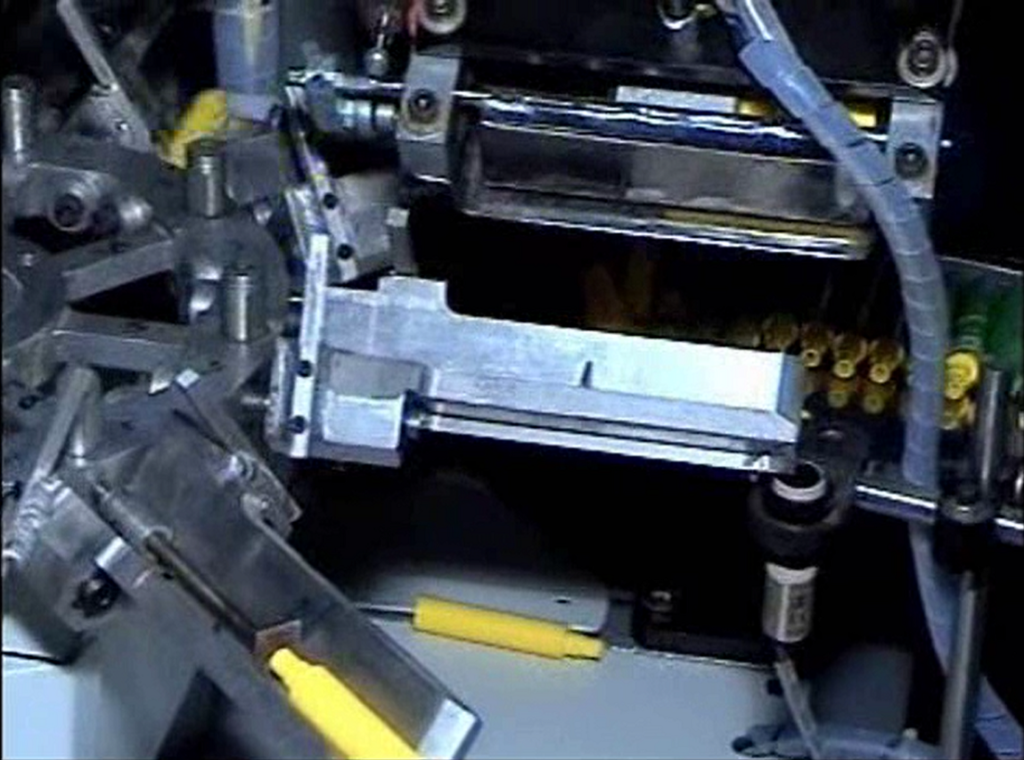