Ultra-Light Weight Vacuum Chambers
A quantum leap towards improving the viability of vacuum cooling technology
By Harshavardhan Sripathi, Director Operations, Innomation
Introduction
The fundamental scientific principles underlying Vacuum Cooling technology have been known for decades, and the technology is recognized as highly versatile, with applications in a variety of industries such as bread & baked goods, meat & poultry, vegetables & herbs, flowers, turf and even compost. It offers significant advantages such as, ultrafast cooling, longer shelf life and better product quality, when compared to traditional cooling methods. Moreover, with advances in energy recovery technologies, modern vacuum coolers consume significantly less energy when compared to traditional cooling methods such as blast freezers and cold rooms.
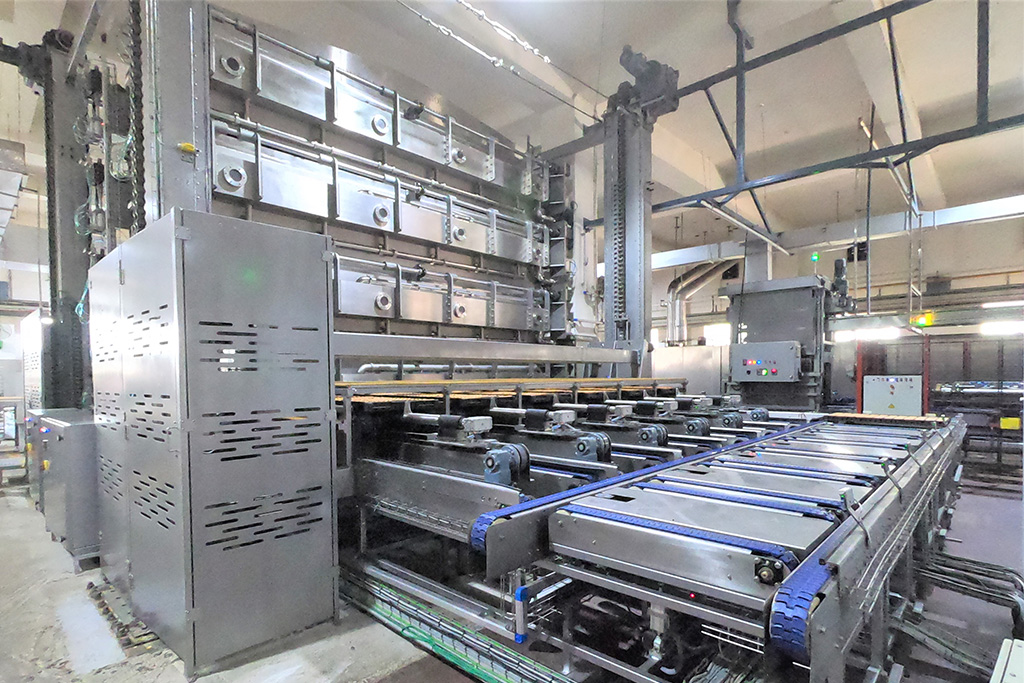
So why is vacuum cooling not ubiquitous?
Although Vacuum Cooling technology has significant benefits, adoption has been slow, and traditional cooling installations still vastly outnumber vacuum cooling systems. One of the main reasons behind its low market penetration is the significant initial investment required, which in some cases, can be up to 25% of the overall plant equipment cost. The major component of the cost of a vacuum cooling system, is the vacuum chamber, which needs to be extraordinarily strong to sustain the forces generated during vacuum and can consume up to 50% of the overall project material cost.
What makes a vacuum chamber so expensive?
Typically, an online vacuum cooling system for an industrial bread plant, with a capacity of 50 metric tons per day, would consist of 4 to 5 rectangular vacuum chambers. Each chamber would weigh around 25 tons with approximately 6-meter width by 2.5-meter depth by 0.5- meter height. Due to the rectangular design, the walls of the chamber need to be extraordinarily thick to ensure that the chamber does not collapse under vacuum. To put things in perspective, the top and bottom sides of the above rectangular chamber, under vacuum, will need to withstand a force of approximately 150,000 kg i.e., 25 adult African elephants on each side!
In engineering terms, a rectangular chamber has the lowest strength / weight ratio, and the highest surface area / volume ratio, when compared with a curvilinear or a cylindrical structure. i.e., rectangular vacuum chambers are inherently inefficient structural designs and therefore expensive.
Innomation’s engineers have designed and patented a novel vacuum chamber structure, that is stronger than the existing rectangular vacuum chambers, while being a fraction of their weight, and consequently were able to reduce the chamber material cost by 70%.
How can you make these vacuum chambers at a fraction of the cost?
In terms of structural strength per unit weight, a cylindrical structure is far stronger than a rectangular structure. However, designing the entire 6-meter-wide chamber in a cylindrical shape would require the chamber to be of 6-meter height as well, and this would greatly increase the overall space required for the vacuum cooling system. To get around this, our engineers decided to divide the width of the chamber into 6 parts and combine 6 cylinders of 1 meter diameter to form a 6-meter-wide chamber. These 6 individual cylindrical chambers were combined with a common curvilinear duct on both sides which served as a base for the entry and exit doors. This novel structural design reduced the chamber weight, from 25 tons to 6.5 tons, thereby reducing the material cost by approximately 70%.
Further, our modular cylindrical vacuum chambers provide the following inherent advantages.
- Higher-strength minimizes the chances of implosion under vacuum and improves safety.
- The cylindrical shape allows automated flushing of the chambers, greatly enhancing hygiene.
- Modular construction allows the system to automatically bypass any chambers that have developed leaks or are under maintenance and run production on the remaining chambers. This improves the availability and flexibility of the system.
- Modular construction allows both horizontal and vertical stacking of vacuum chambers, reducing the overall footprint area required.
- Modular construction allows easy transportation of these chambers in dismantled conditions, even in difficult terrain.
This simple patented innovation, which is a result of our first-principles approach towards design, greatly improves the viability of vacuum cooling technology.